If you're researching metal laser cutting, laser cut metal, laser cutting metal, metal laser engraving, or laser engrave metal, you're in the right place. Modern laser systems empower creators to both cut durable metal parts and engrave intricate designs—all from the same setup.
In this guide, you'll learn:
- The key differences between metal laser cutting and engraving
- Which metals and laser types work best
- Recommended settings per material and process
- Inspirational project ideas for makers and small businesses
- Maintenance, safety advice, and common issues with solutions
🔍 1. Cutting vs Engraving Metal: What’s the Difference?
- Metal Laser Cutting uses high-powered fiber lasers (sometimes with nitrogen or oxygen assist) to cut fully through sheet metal, ideal for parts, signage, and industrial prototypes.
- Metal Laser Engraving etches the surface—great for branding, fine details, or decorative patterns. Fiber or MOPA lasers enable that precise marking.
Many creative workflows merge both: cut the shape first, then engrave logos or decorative elements for a high-end finish.
🧰 2. Compatible Metals & Laser Types
Supported Materials:
- Stainless Steel
- Aluminum
- Brass
- Titanium (requires specialized lasers like fiber or MOPA)
Laser Types:
- Fiber Lasers: Efficient and precise for cutting or engraving bare metal.
- MOPA Lasers: Allow adjustable pulse to enable multicolor or high‑contrast marks.
- CO₂ Lasers: Rarely used for metal unless you apply special coatings or use engraving sprays, and even then results are limited.
⚙️ 3. Recommended Settings for Metal Work
Cutting Metal:
- Use fiber laser power between 500 W and 1500 W, depending on thickness.
- Speeds, assist gas flow, and focus distance vary—always conduct test cuts.
- Use nitrogen for aluminum (oxidation-free) and oxygen for steel (faster cutting).
Engraving Metal:
- Use 20–100 W fiber or MOPA lasers.
- Sample speeds: Stainless steel: 80–120 mm/s; Aluminum/brass: adjust frequency for visual contrast.
- Aim for 300–500 DPI for detailed engraving.
- Perform trial runs using scraps to fine-tune power/speed.
🎨 4. Creative Project Ideas for Makers & Small Businesses
- Custom metal signage (stainless or aluminum)
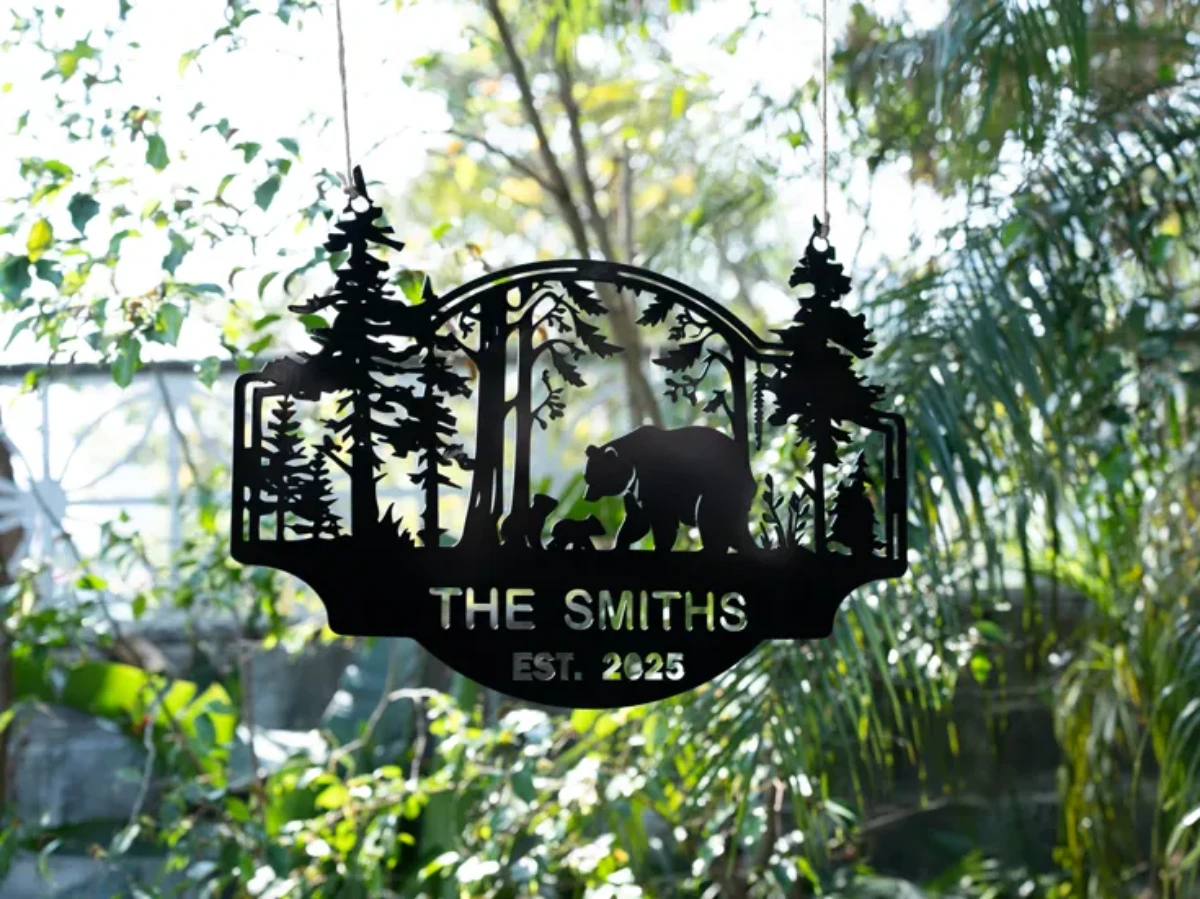
- Engraved metal keychains or bottle openers
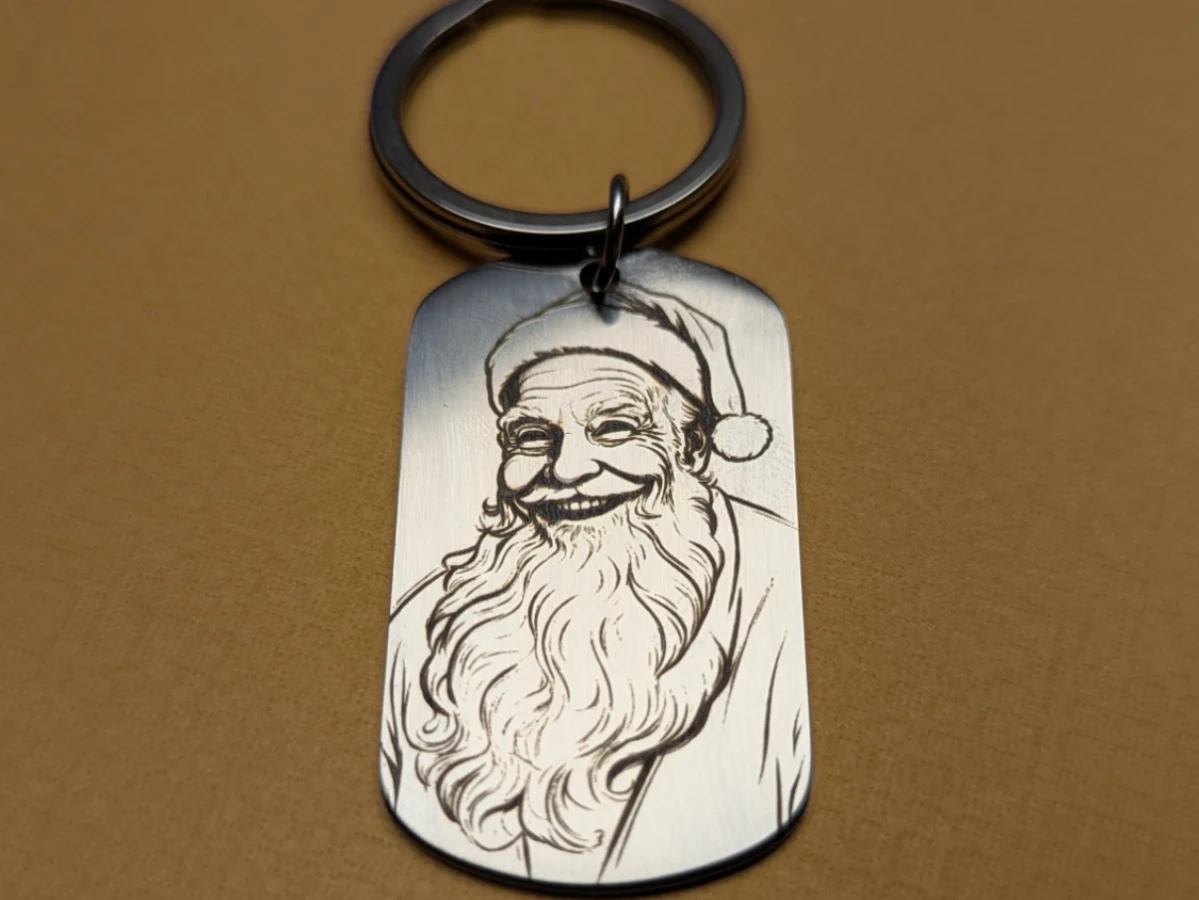
- Lapel pins or metal jewelry pieces with engraved logos or patterns
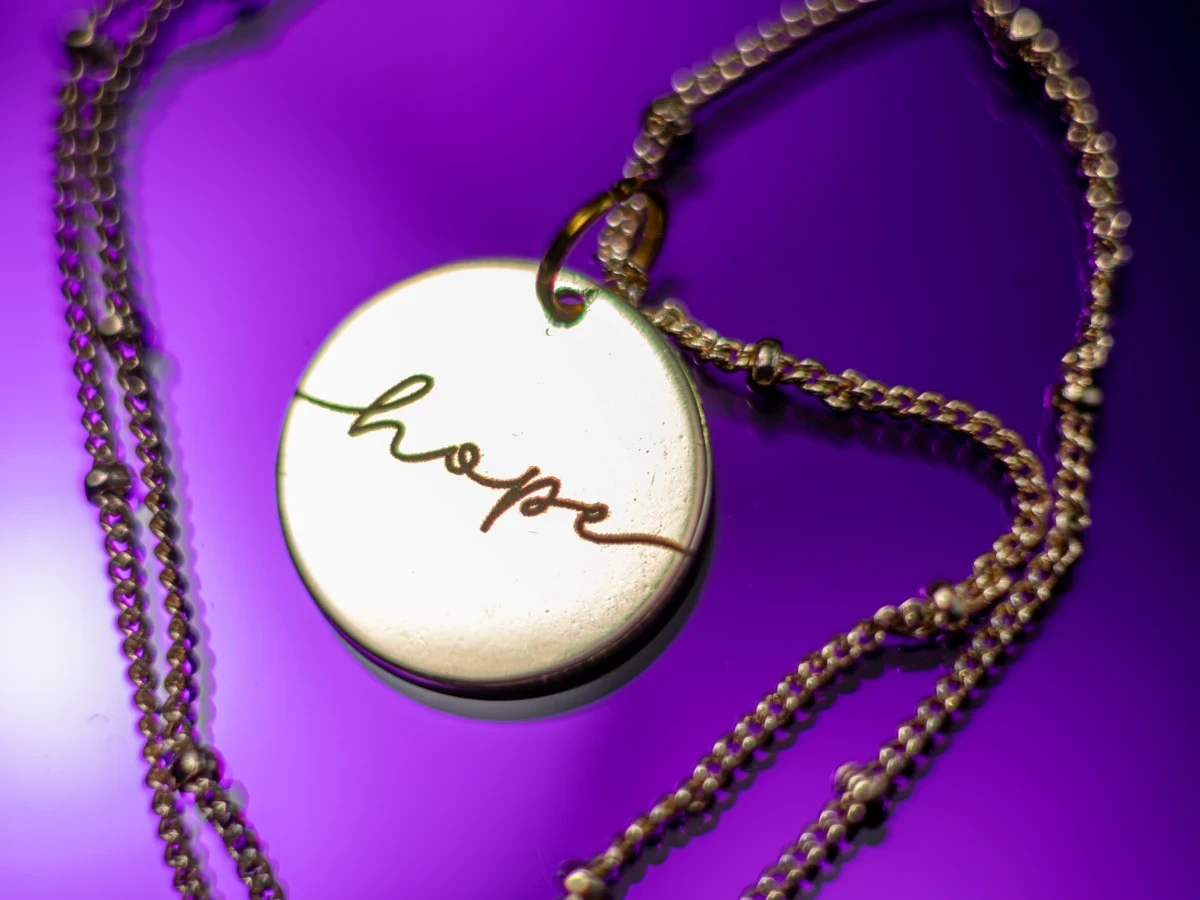
- Award plaques or branded desk accessories
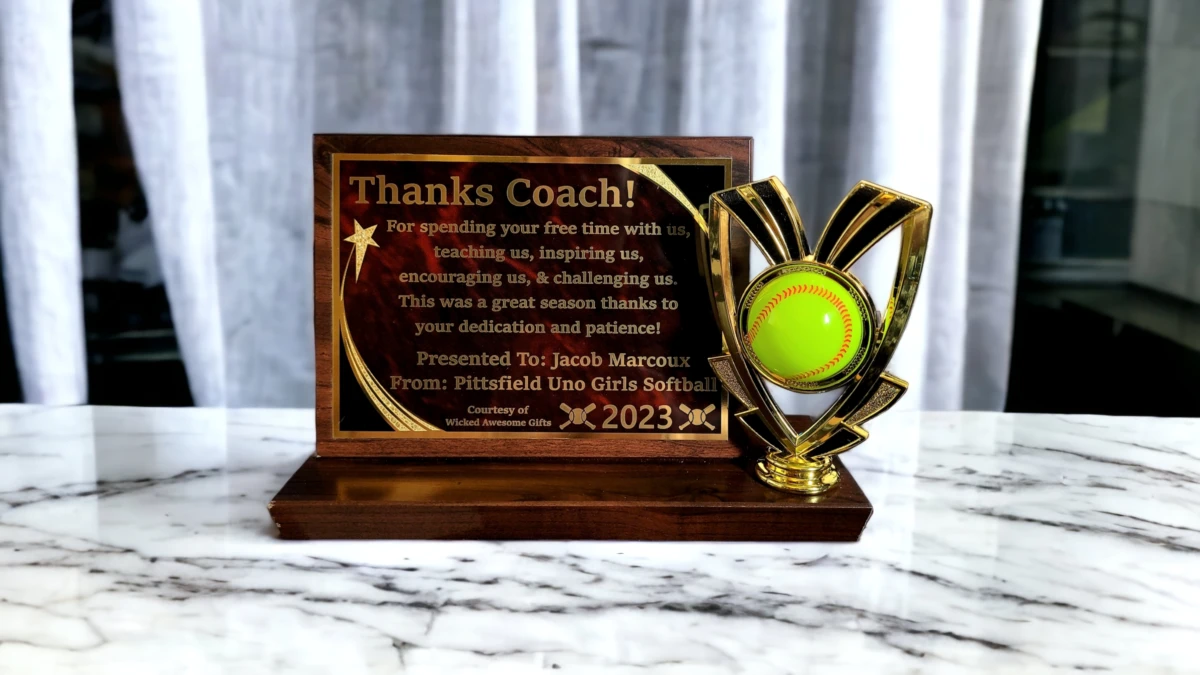
- Tool tags or identification plates with engraving
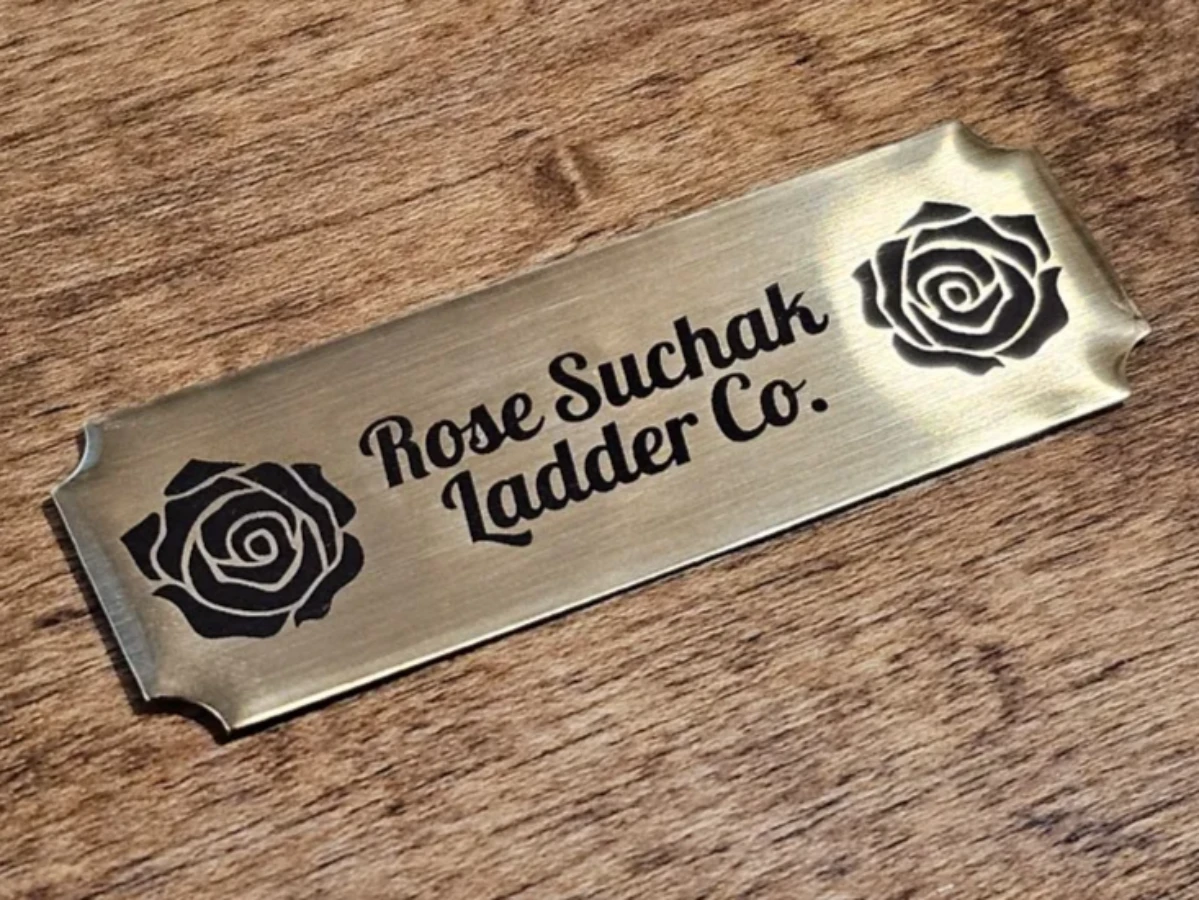
Explore More Metal Projects
Pro Tip: Combine engraving and cutting—e.g., laser-cut nameplate engraved with a company logo.
🛡️ 5. Maintenance & Safety Tips
- Ensure solid ventilation to manage metal dust and fumes.
- Keep lenses and mirrors clean—dirty optics degrade beam focus and cut quality.
- Wear IR-rated eye protection when operating fiber lasers.
- Align optics every 50–100 hours or if quality degrades.
- Monitor assist gas purity and flow rate—it directly affects edge finish.
⚖️ 6. Common Issues & Solutions
- Incomplete cuts or weak engraving → likely low power or misaligned optics.
- Burn marks or discoloration → too much laser power, slow feed rate, or poor gas flow.
- Faint engraving → resolution too low or using wrong metal/laser combination.
- Reflective surface reflections (in diode/CO₂ setups) → use fiber/MOPA models and proper focusing technique.
❓ FAQ – Laser Metal Cutting & Engraving
Q: Can one machine do both cutting and engraving metal?
Yes—most fiber laser systems support both operations by adjusting power, speed, and beam focus.
Q: Is a CO₂ laser suitable for cutting metal?
Generally not. It's primarily for non-metals. Some coated metals can be lightly engraved or cut with gas assist, but it's inefficient and less precise.
Q: What’s the main difference between laser engraving and cutting metal?
Engraving removes only surface material. Cutting penetrates the full thickness to separate pieces from a sheet.
Q: How safe are metal lasers for small workshops?
Safe—if you use proper ventilation, wear protective eyewear, and never leave the machine unattended during operation.
✅ Conclusion & Next Steps
Laser cutting and engraving metal unlocks high precision and creative flexibility—from practical signage and industrial parts to artisan jewelry and branded decor. This single workflow balances both technical and artistic needs.